Closing the lobster traceability gap
Atlantic Lobster comes from one of the most sustainable fisheries in the world. But can the seafood processors and seafood exporters of this remarkable product actually prove it?
Complex traceability for frozen and processed lobster
The Atlantic lobster industry has made great strides in recent decades in establishing itself as one of the most environmentally sound and sustainable fisheries out there, with many undergoing the stringent requirements of MSC certification. Indeed, the value of Canadian lobster exports topped $3.2 billion last year — the highest ever and more than $700 million higher than pre-pandemic levels, according to new trade data.
For live lobsters, the traceability chain is fairly direct. For frozen and processed lobster products, however, which account for over 60% of the overall export value, traceability is far more complex. This complexity necessitates the use of advanced seafood traceability software and seafood processing software to ensure accuracy and compliance.
When the Canadian Lobster Council first introduced its Lobster Traceability Pilot Project in January, 2015, it identified a number of challenges facing the Atlantic Canada lobster industry in implementing seafood traceability systems. These systems are needed to verify, both for consumers and for regulatory purposes, that the lobster being sold is indeed what the label says it is. Moreover, adherence to FDA seafood labeling requirements and general seafood labeling requirements is crucial for maintaining market trust and regulatory compliance.
The challenges include:
- Relatively high number of suppliers and consequently high number of data entries, which can be managed more efficiently with fish processing software.
- A single finished product can contain lobster from multiple suppliers, making fish traceability essential.
- Need to extend a batch (lot) production over several days, which can be streamlined with seafood processing solutions.
- Tracking of lobster throughout complex production processes, from harvest to export, requiring robust seafood distribution software.
- Tracking lobsters in holding pond, a task that can be facilitated by seafood traceability software.
The seafood logistics involved in the export process also add layers of complexity. Assessment and management of seafood safety and quality are critical to ensuring that the products meet international standards. The importance of a trace register for seafood cannot be overstated, as it helps in maintaining a transparent supply chain and supports the overall fishery export process.
The advancements in seafood processing solutions have thus become indispensable tools for the industry, enabling better management of seafood export logistics and adherence to regulatory standards.
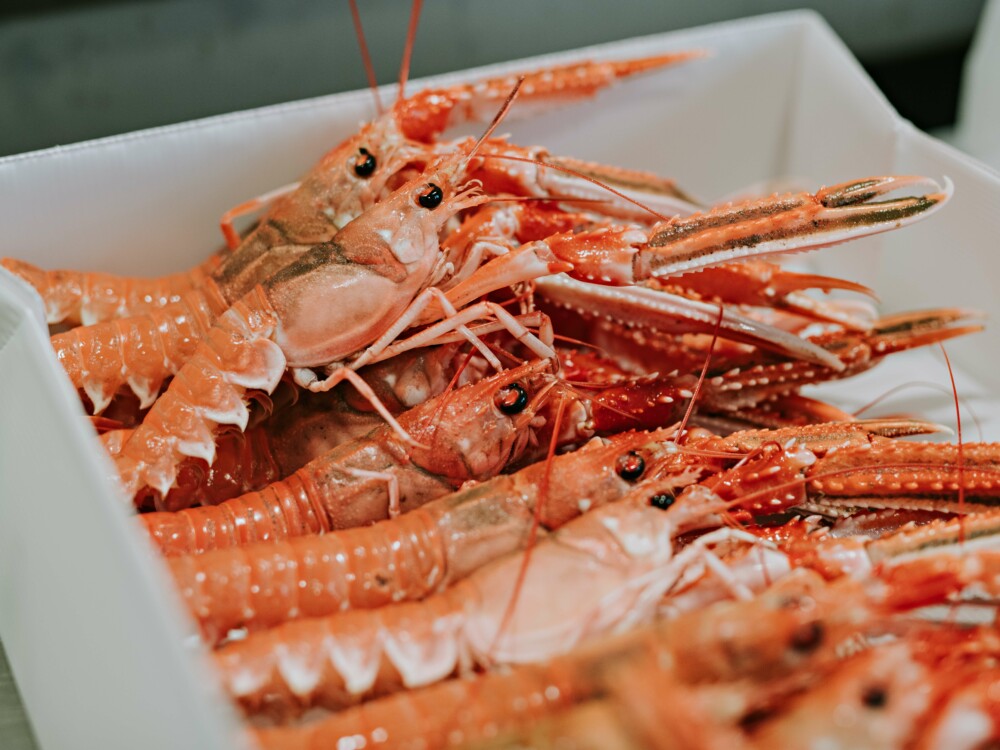
Broader opportunity for lobster operations
Past attempts to adopt digital seafood traceability systems throughout the lobster value chain have been both significantly expensive and cumbersome to put into operation, with long and inflexible implementation cycles and costly customizations. Maritech’s cloud based seafood ERP software are changing all that and now include new modifications tailored for the lobster industry. The new seafood software is drawing broad attention from seafood producers, exporters, and processors of all sizes and within all segments – large global corporations as well as smaller companies.
The launch of our cloud based seafood ERP software, has really meant that sophisticated digital systems that would once have been out of reach for small operators are now readily available with absolutely no huge up-front capital costs and complex IT implementation cycles. This advancement supports better seafood traceability, ensuring compliance with seafood labeling requirements and FDA seafood labeling requirements. The availability of such solutions is transforming the seafood logistics involved in lobster processing and export, making it easier for businesses to manage the assessment and management of seafood safety and quality.
A new era of lobster business
There is no doubt that for many companies, new cloud based seafood software with digital traceability systems can lead to a considerable increase in efficiency and profitability. As well as other positive effects, such as improved sustainability, easier reporting, and reduced manual workloads.
Now it is easier than ever for companies to get started. At Maritech, we have many examples on successful seafood digitalisation projects, one of our small Maritech Purchase and Sales software customers, who is based in New Jersey, was fully set up and running our software to manage international seafood sales operations within the space of a week. In addition to our core Purchase and Sales, we provide integrations to our own solutions with labeling and packing systems, our new cloud based Transport Management System for logistics and transport companies, quality tracking, claims, and IoT.
This kind of flexibility is revolutionizing the way lobster companies can now do business, making it easier to comply with FDA seafood labeling requirements and general seafood labeling requirements, while enhancing seafood traceability and improving the assessment and management of seafood safety and quality.